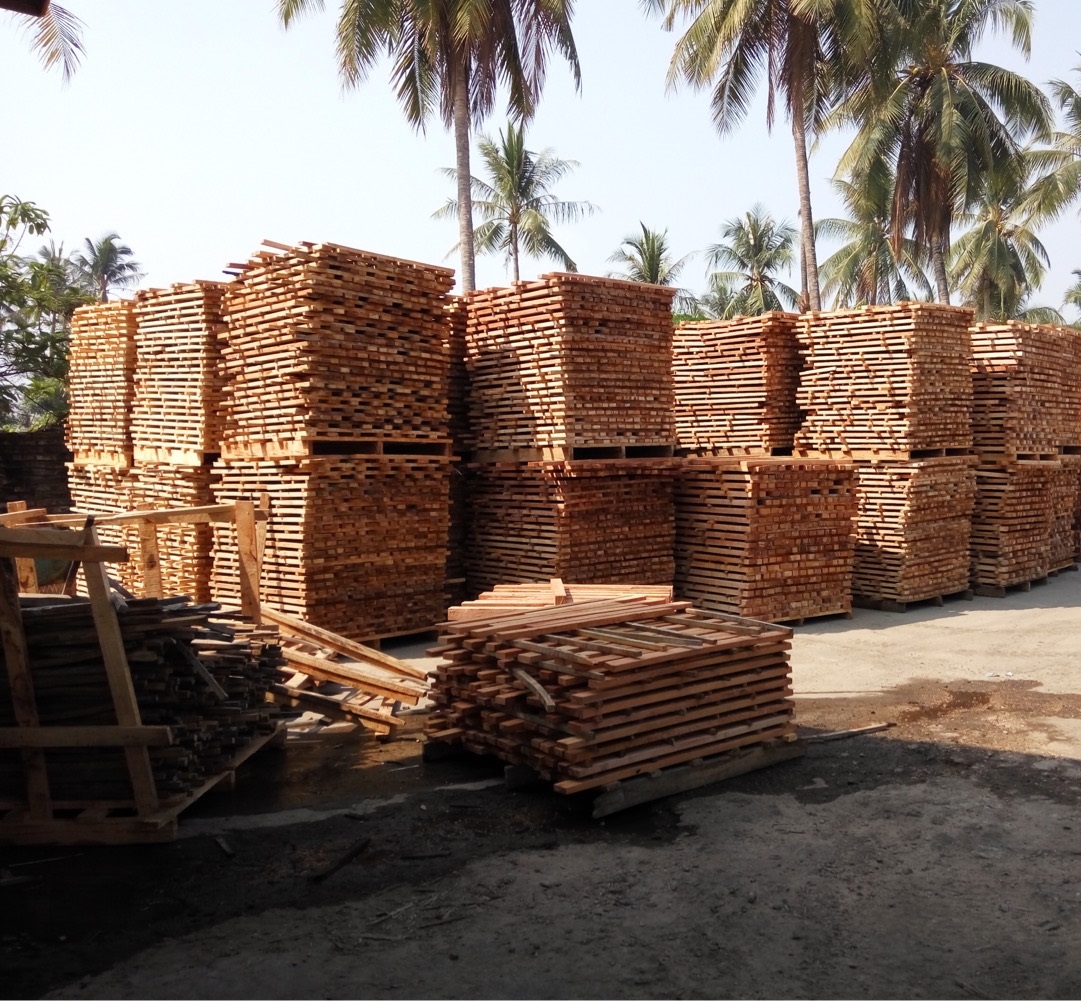
Rubberwoods
Rubberwood is a light-colored medium-density tropical hardwood obtained from the Pará rubber tree (Hevea brasiliensis), usually from trees grown in rubber plantations. Rubberwood is one of the more durable lumbers used in the manufacturing of today’s home furnishings. Rubberwood has a dense grain character that is easily controlled in the kiln drying process. Rubberwood has very little shrinkage making it one of the more stable construction materials available for furniture manufacturing. Like maple, rubberwood is a sap producing species. In the case of maple, it is sap; in the case of rubberwood, it is latex. Rubberwood produces all the latex used in the world for all rubber based products. There is one more important feature of rubberwood that is very important in today’s world. Rubberwood is the most ecologically “friendly” lumber used in today’s furniture industry. After the economic life of the rubber tree, which is generally 26-30 years, the latex yields become extremely low and the planters then fell the rubber trees and plant new ones. So, unlike other woods that are cut down for the sole purpose of producing furniture, rubberwood is used only after it completes it’s latex producing cycle and dies. This wood is therefore eco-friendly in the sense that we are now using what was going as waste.
Rubberwood furniture manufacturing process
Rubberwoods are being processed and treated in a typical standard wood process before usage in various industries. There are essentially 6 key steps to manufacture rubberwood furniture.
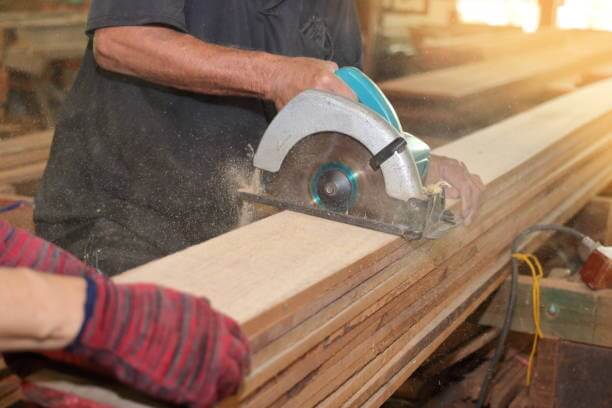
(1) Cutting
Raw rubberwood harvested are then immediately transported to the processing factory to be treated as rubberwood are prone to bacteria infection and fungi growth.
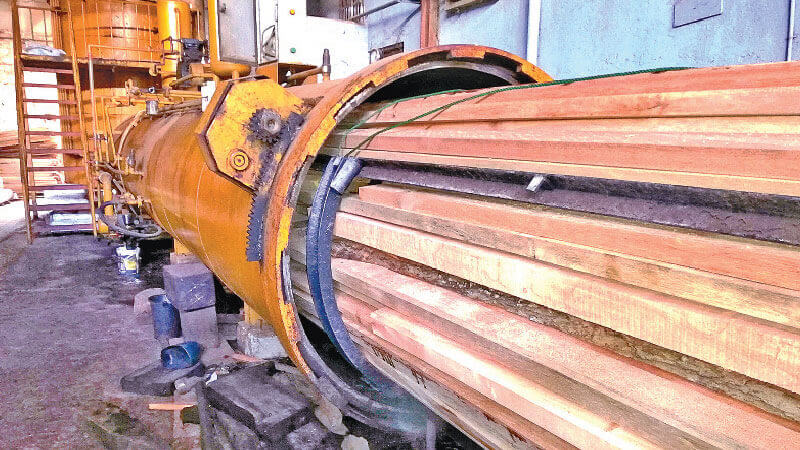
(2) Pressurized Preservation Treatment
The raw rubberwood sawn timbers are placed in a pressure chamber, where they are injected with a liquid chemical compound that will prevent decay and protect them from termites. The pressure chamber is vacuum sealed and then filled with liquid chemical preservatives. The pressure is increased until it reaches 5 -11; 10 kg m -3 and is kept at this setting for 20 minutes.
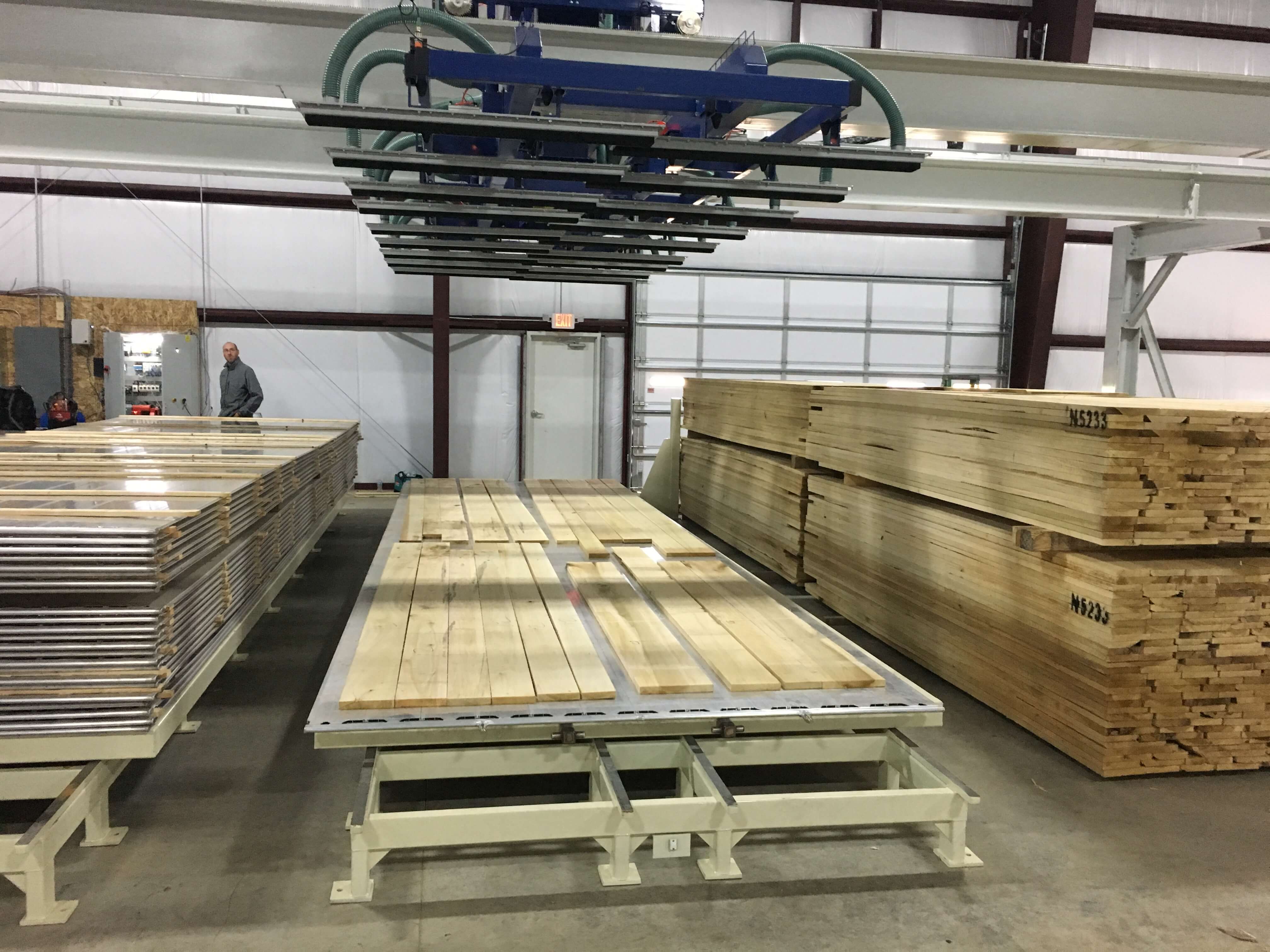
(3) Kiln Drying
The drying process is done in a kiln, where excess moisture is removed, leaving the rubber wood with a uniform moisture level. Drying the rubber wood in a kiln helps prevent the surface from cracking and splitting that acure when the wood is left to dry naturally. Kiln drying increases the strength of the rubber wood as well as making it lighter and less costly to transport.
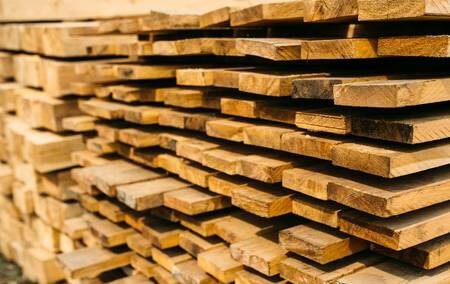
(4) Sizing and Sorting(Quality Controls)
Rubberwood are being carefully inspected for its flaw after the treatment process to ensure quality. Each piece of wood will be resized and sorted as accordingly after the property inspection done by qualified personnel.
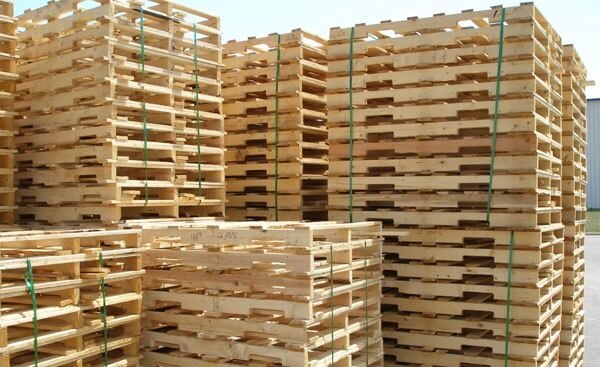
(5) Packaging
A quality packaging process is used to ensure that the processed/treated rubber wood retains its freshness after it has been processed. We package it by stacking it in cubic meter bundles, wrapped in waterproof wrappers. This quality and standard packaging process is adopted by the company to prevent water seepage and staining.
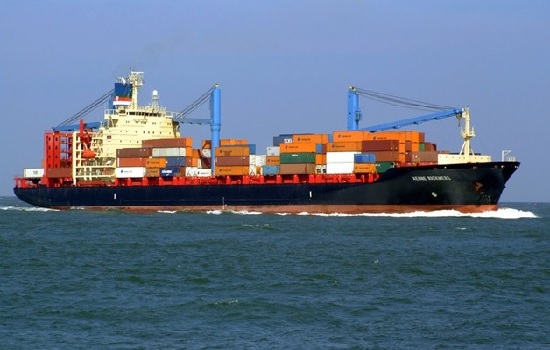
(6) Fumigating and Shipping
Rubberwood will be fumigated as required by the Agricultural Department of Myanmar in order to enable its protection from bacteria and fungi infection. This will be done in a simple spraying of the chemical to the rubberwood. Finally, the rubberwood is ready to be shipped to the specific locations!